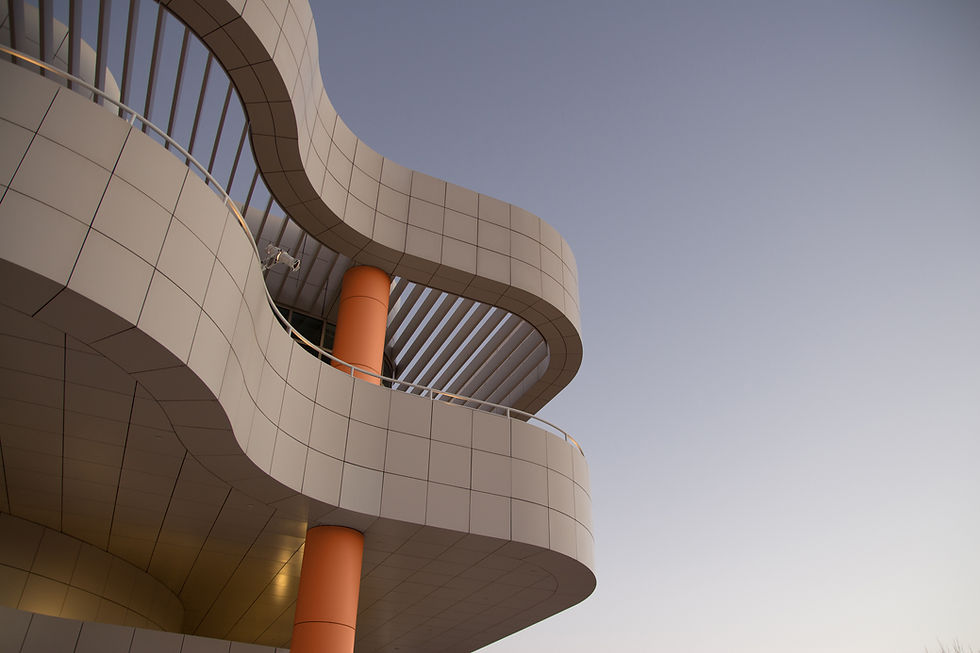
10 Key questions to ask when unlocking sustainable solutions
Jun 10, 2024
3 min read
0
0
0

Here are 10 key questions to ask when unlocking sustainable solutions through analytical rigor and creative thinking:
What are the root causes driving the problem or suboptimal performance? Have we dug deep enough to uncover the underlying issues?
How will addressing this challenge impact the broader system or operation? Have we considered potential downstream effects and interdependencies?
What data and analytical tools do we have access to that can provide deeper insights into the problem? Are we leveraging all relevant sources of information?
Have we engaged with key stakeholders, subject matter experts, and frontline operators to gain a comprehensive, multifaceted understanding of the challenge?
What innovative, out-of-the-box solutions can we explore to address the root causes, rather than just treating the symptoms?
How can we design solutions that not only resolve the immediate problem, but also set the stage for long-term, sustainable improvement?
What potential risks or unintended consequences should we be aware of, and how can we proactively mitigate them?
What capabilities, resources, or partnerships do we need to successfully implement and maintain the proposed solutions?
How can we foster a culture of continuous learning and improvement to ensure that our problem-solving approaches remain agile and effective over time?
What key performance indicators or success metrics should we track to measure the ongoing impact and effectiveness of our solutions?
By consistently asking these types of probing, holistic questions, organizations can cultivate a problem-solving mindset that is grounded in analytical rigor, creative thinking, and a relentless commitment to sustainable outcomes. This approach empowers teams to transform complex challenges into opportunities for growth, innovation, and long-term competitive advantage.
Let's apply the proactive problem-solving approach to minimizing machine downtime in a plant. Here are the 10 key questions to consider:
What are the root causes driving machine downtime in your manufacturing plant? Have you analyzed maintenance records, production data, and operator feedback to uncover the underlying issues?
How does machine downtime impact your overall production efficiency, product quality, delivery timelines, and financial performance? Have you evaluated the end-to-end implications across your operations?
What data do you have access to (machine sensors, maintenance logs, production schedules, etc.) that can provide deeper insights into the causes and patterns of downtime? Are you leveraging all relevant data sources?
Have you engaged cross-functional teams, including maintenance technicians, production operators, and engineering experts, to gain a comprehensive understanding of the downtime challenges and potential solutions?
What innovative approaches (predictive maintenance, autonomous monitoring, enhanced operator training, etc.) could you explore to address the root causes of downtime, rather than just reacting to issues as they arise?
How can you design a proactive maintenance strategy that not only minimizes immediate downtime, but also enhances the long-term reliability and performance of your manufacturing equipment?
What potential risks (supply chain disruptions, budget constraints, workforce issues, etc.) should you be aware of, and how can you proactively mitigate them to ensure the sustainability of your downtime reduction efforts?
What capabilities, resources, or partnerships do you need to successfully implement and maintain your proactive maintenance program (e.g., specialized technologies, technical expertise, vendor collaborations)?
How can you foster a culture of continuous improvement and shared ownership around machine reliability within your manufacturing plant? How can you empower teams to identify and address downtime issues proactively?
What key performance indicators (e.g., mean time between failures, overall equipment effectiveness, maintenance cost per unit) should you track to measure the ongoing impact and effectiveness of your downtime reduction solutions?
By systematically working through these questions, you can develop a comprehensive understanding of the downtime challenges in your manufacturing plant, identify innovative solutions that address the root causes, and create a roadmap for implementation and continuous improvement.
This proactive, data-driven approach will not only help you minimize machine downtime, but also enhance your overall operational efficiency, product quality, and financial performance.
Remember, the key is to remain curious, collaborative, and committed to sustainable outcomes. With this mindset, you can unlock transformative solutions that drive long-term value for your business and your customers.